“…Me sorprende como es que se arma el coche. Los técnicos solo toman las piezas de los racks y las van colocando una tras otra, es como si fuera un Lego® gigante…”
Este fue más o menos el comentario que me hizo un practicante, la primera vez que lo lleve a una la línea de ensamble, de la armadora donde trabajaba.
A primera vista, puede parecer sorprendente que todas esas piezas de formas y características complejas se ensamblen unas con otras sin presentar complicaciones, hasta formar un coche (o cualquier otro producto mecánico). La realidad es que se trata del resultado de un gran trabajo en equipo de un sin número de especialistas de diferentes áreas técnicas, financieras y administrativas, por mencionar solo algunas.
Una de las disciplinas que se encarga de garantizar que el producto se pueda armar y, además, “que se arme bien”, es el Dimensional Management.
El Dimensional Management es una metodología de diseño y optimización de productos, que se utiliza para “alinear» los requerimientos de función y calidad del producto, con las capacidades de manufactura y ensamble; de esta forma, se logra la fabricación del producto como esperado, respetando los criterios financieros establecidos.
Esta alienación se logra principalmente estimando y analizando la acumulación de variación, que se genera por la desviación dimensional de los componentes, y que se distribuye en el producto a través de las secuencias de ensamble.
Cuando se conoce la acumulación de variación, se compara con los niveles de aceptación establecidos para las características de función y calidad. Así se determina si el diseño, en combinación con los procesos de manufactura y ensamble planeados, son adecuados para la fabricación del producto.
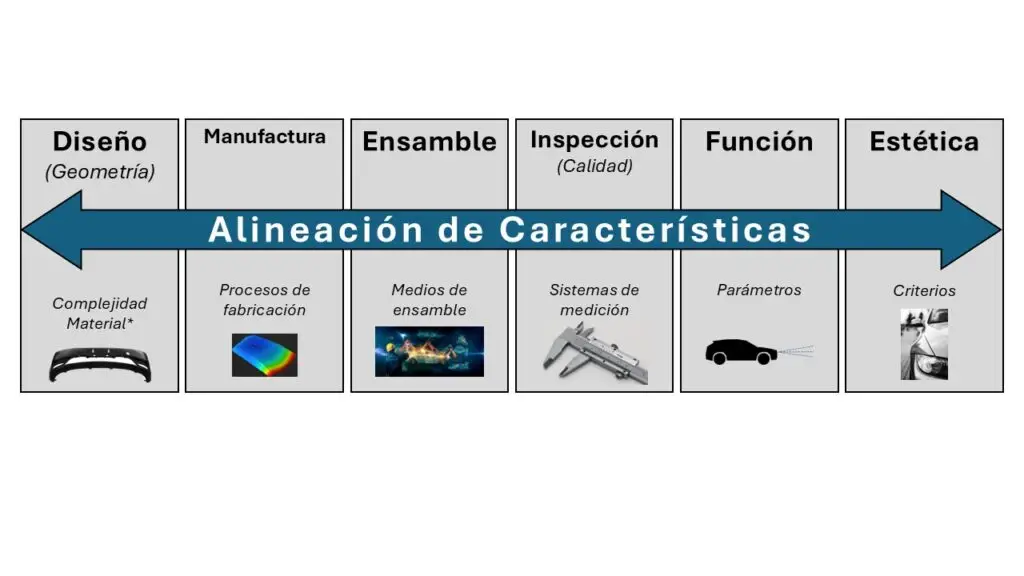
Para calcular la variación de ensambles y componentes, se utilizan diferentes técnicas y metodologías, como la implementación del tolerado geométrico y dimensional, el diseño de experimentos, el análisis de tolerancias o “Tolerance Stack up” , técnicas de simulación por elemento finito y control estadístico de procesos. Con este “kit de herramientas”, se calculan diferentes escenarios potenciales de producción, que son evaluados por un equipo multidisciplinario, para encontrar la combinación optima de parámetros y características de diseño, manufactura, inspección y ensamble, que darán como resultado el mejor producto posible.
El equipo multidisciplinario es muy importante, pues dentro de este gremio, se llevarán actividades como:
- Recolección de información para efectuar los análisis de variación.
- Cambios de ingenieria al producto o proceso.
- Acuerdo sobre soluciones técnicas.
- Acuerdos de tolerancias de componentes y productos, para liberación técnica.
- “Briefings” para escalación de acuerdos.
- Transmisión de la información y acuerdos a los especialistas de cada área.
Esta metodología se utiliza tanto en el desarrollo de productos nuevos, así como en aquellos que ya se encuentran en producción, a través de programas de mejora continua y optimización. Aunque su aplicación es similar en ambos escenarios, en este articulo hablaremos de la implementación en el desarrollo de un producto, y en un artículo próximo, abordaremos su aplicación en procesos de optimización.
Implementación del Dimensional Management
Fase 1: Presentación del producto e integración del equipo multidisciplinario.
Se integra un equipo con representantes de las áreas involucradas (calidad, producción, desarrollo de producto, etc.).
Se presenta la información sobre el producto, así como características específicas a considerar; por ejemplo: versiones que estarán disponibles al mercado, nuevas tecnologías que se integrarán al producto, etc.
Fase 2: Definición de objetivos y/o alcances
El equipo de trabajo analiza la información proporcionada y acuerdan las características clave del producto, para “traducirlas” en especificaciones técnicas, que, a su vez, se convertirán en requerimientos técnicos para los componentes individuales.
Fase 3: Recolección de información para análisis.
Los representantes de cada área entregan información sobre los procesos de manufactura y ensamblé, así como las primeras geometrías (modelos CAD), que se tienen disponibles para que se inicien las actividades de cálculo de variación.
Fase 4: Estimación de variación, fallas potenciales y propuestas de solución.
Utilizando la información recolectada, se realiza el primer análisis de variación, mostrando los resultados que incluyen; 1) el nivel o probabilidad de cumplimiento de los requerimientos del producto, 2) problemas potenciales de montaje y 3) alternativas de solución, que deberán de ser acordadas por el equipo.
Esta etapa representa la mayor parte de las actividades del Dimensional Management, pues se trata de un proceso iterativo donde se analizan propuestas y alternativas, hasta encontrar la mejor solución en términos financieros, técnicos y de calidad.
En esta etapa se comienza a generar la información técnica dimensional del producto, y se actualiza según se van logrando acuerdos y resolviendo las fallas detectadas.
Fase 5: Cierre de actividades y Liberación técnica.
En esta etapa, los acuerdos y soluciones ya se han aplicado o se encuentran proceso de implementación. Cuando todos los cambios están implementados, los componentes se consideran liberados técnicamente, lo que asegura que, al fabricarse y ensamblarse según la información técnica, el producto final no tendrá problemas de montaje y cumplirá con las especificaciones clave.
La fase finaliza con la presentación de los resultados estimados del producto, incluyendo el cumplimiento de los requisitos y el estado de las actividades realizadas. Toda la información se documenta como lecciones aprendidas, instrucciones de montaje y directrices de diseño para futuros proyectos, y el equipo se disuelve.
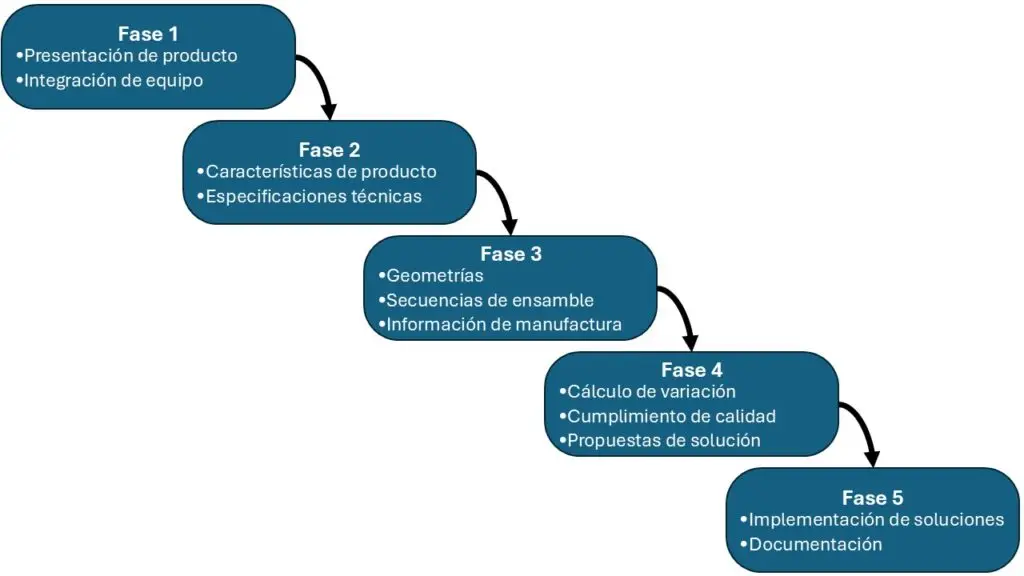
Soporte posterior a la etapa de desarrollo
Aunque el equipo ya no se encuentra activo, los especialistas encargados del análisis de variación continúan dando soporte al proceso de arranque de manufactura. En caso de que se presenten cambios o condiciones no previstas durante el desarrollo, aunque las soluciones en esta etapa se tratan directamente con los involucrados.
Beneficios y consideraciones:
Beneficios generales:
- Establece una política objetiva de solución de problemas enfocada en el producto.
- Minimiza el riesgo de problemas de montaje e incumplimiento de calidad de producto terminado.
- Optimiza los tiempos de desarrollo, por medio de un enfoque centralizado en las características que afectan las características de calidad.
- Ayuda al proceso de diseño de manufactura e implementación del sistema de gestión de calidad, por medio de la definición clara de las características clave de los componentes.
- Ahorro de costos por el desperdicio de material y reducción de riesgos financieros relacionados con los retrabajos por ensamble.
- Ayuda a reducir los tiempos de lanzamiento de productos
- Establece la plataforma de implementación de herramientas avanzadas como los Gemelos Digitales o Fabricas Virtuales.
Beneficios específicos para OEM´s
- Permite validar diseños y asegurar la factibilidad del producto desde etapas tempranas.
- Establece requerimientos técnicos específicos y claros para sus proveedores Tier 1.
- Garantiza la intercambiabilidad de componentes de fabricación propia y de diferentes proveedores Tier 1.
Beneficios específicos para Empresas Tier 1:
- Permite cumplir con las especificaciones del cliente minimizando e incluso evitando cambios a su capacidad instalada.
- Le permite establecer procesos de optimización y mejora continua más efectivos para mantenerse competitivos en el mercado.
- Le brinda un soporte efectivo y eficiente para el desarrollo de documentación mandatoria como AMEFs de producto y proceso, para facilitar la implementación de sus Sistema de Gestión de Calidad.
Consideraciones
- El personal debe de contar con capacitación adecuada en la implementación de metodologías de tolerado dimensional y geométrico, así como en la identificación de características clave del producto.
- Los análisis de variación se deben de realizar según la complejidad del producto.
Conclusión
El Dimensional Management no solo es una metodología, sino una estrategia esencial para garantizar calidad, reducir costos y aumentar la competitividad. Tanto los OEMs como las empresas Tier 1 pueden beneficiarse de su implementación, especialmente cuando está respaldada por herramientas avanzadas y capacitación adecuada.